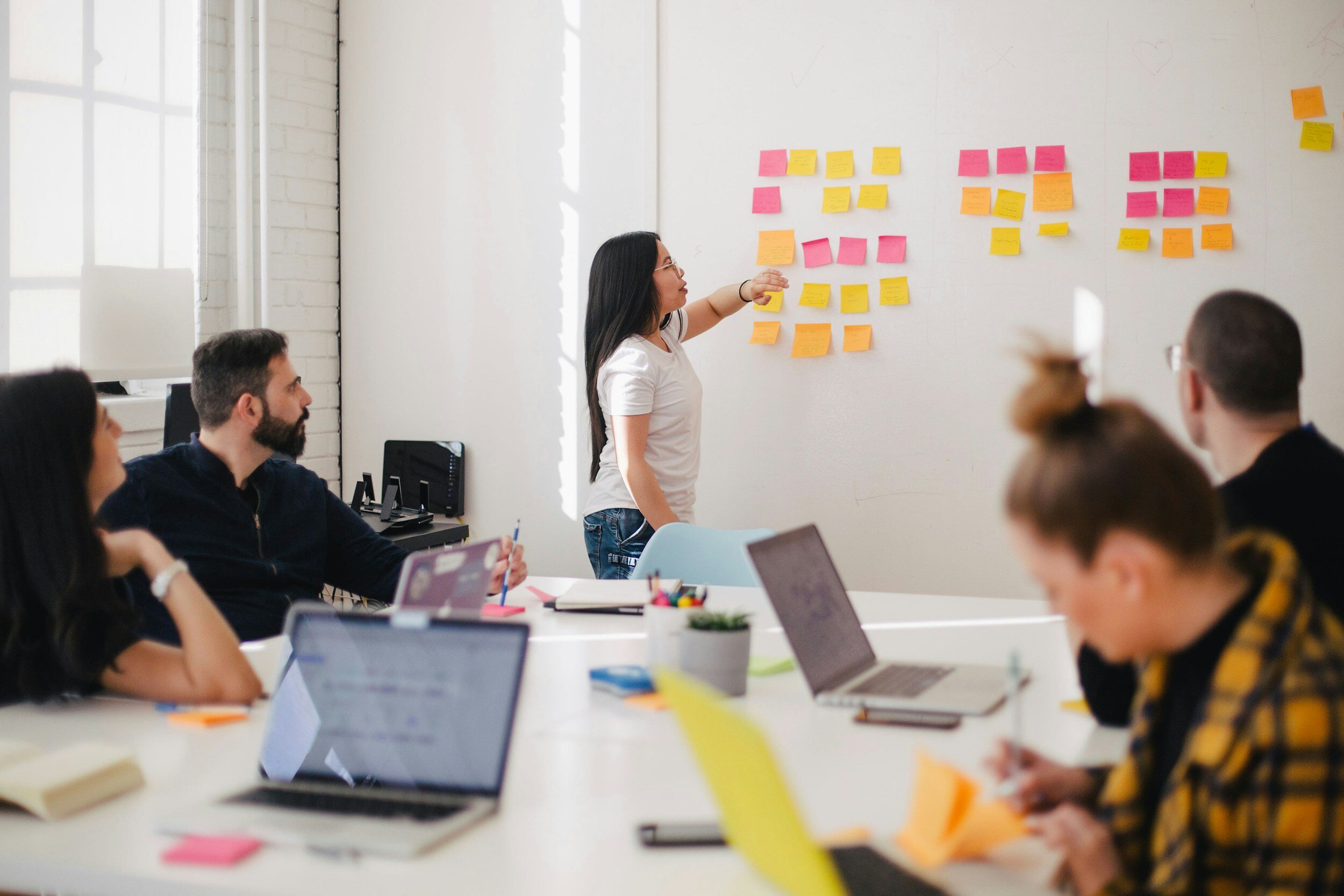
Operations Consulting
Our Methodology
Waste reduction (LEAN and Six Sigma Process Improvement)
Secure leadership commitment and form a cross-functional LEAN team.
Identify specific areas for improvement and set measurable goals.
Map the current process to identify value-adding and non-value-adding activities.
Identify key areas where LEAN improvements can be made, and prioritize them based on impact and feasibility.
Apply LEAN and Six Sigma tools to drive process improvements and eliminate waste.
Improve the flow of materials and products through the system.
Standardize best practices and make performance visible.
Ensure employees are engaged and equipped to sustain LEAN improvements.
Track progress and sustain improvements through data and metrics.
Ensure that improvements are sustained and built upon over time.
Expected Outcomes
Cost savings through improved efficiency and reduced waste.
Reduced waste (lower inventory levels, minimized defects, less waiting time, and fewer unnecessary motions).
Improved process flow and shorter lead times.
Increased productivity and employee engagement.
Higher quality with fewer defects and improved customer satisfaction.
Sustained continuous improvement efforts
Increased Customer Satisfaction
We help you improve operational excellence by:
Reducing Turn-Around-Time
Increasing On-Time Delivery
Implementing Key Performance Indicators
Increased Employee engagement and retention
Increasing your productivity, reducing cost and eliminating waste